Workplace Accidents - What's the Cost
Delving into the true costs of workplace accidents.
Tyler Rynearson
1/24/20245 min read
Workplace accidents are obviously expensive. Not only the primary costs of treating an injured or sick employee, but many injuries are accompanied by many indirect costs that are often not considered or even attributed to these workplace injuries when assessing their total impact. We're going to try to shed some light on the whole of this matter, at least from a financial perspective, so leaders can better understand the true effect that workforce injuries, or God forbid fatalities, can have on their operation.
So, what are the costs? Well, the more obvious costs of workplace accidents are the primary ones. Things like the cost of treatment, regulatory fines, lost time and productivity, and sometimes repair or replacement of damaged equipment.
Treatment & Workers’ Comp.
Treatment costs can include:
· Emergency Room Visit
· Ambulance Ride
· Air Flight
· Medications
· Physician Appointments
· Specialist Appointments
· Physical Therapy
From 2019-2020, the National Safety Council projected that the average expense for workers' compensation claims stood at $41,353.
But we pay high insurance premiums for this reason, right? Won’t workers’ comp. insurance cover those treatment costs if an employee is hurt on the job? Initially, the answer is yes. But the regular costs of coverage are likely to increase as a result. Because let's face it, that’s how insurance works. Although delayed, over time the company will essentially pay all the treatment costs, and more.
Injury claims affect the company’s experience modifier or X-Mod, more correctly known as Experience Modification Rate (EMR), which is used to calculate the company’s insurance costs. This calculation is based on the company’s total cost of claims, compared to those expected of similarly sized companies in the same industry. This expected rate is known as Class Rate and is set by the National Council on Compensation Insurance (NCCI). The final rate is based on the presupposition that historical losses predict future losses.
Do you know what your company’s X-Mod is? Well, the good thing is that it can be positively redirected, and fairly quickly. The historical assessment of a company’s performance, used to calculate this rate, typically only includes the past 3 years. So, this area is a huge opportunity for companies to see RoI from their safety programs, in a relatively short time.
Citations and Penalties
Both OSHA and MSHA adjust (typically raise) penalty thresholds annually. Penalties can vary drastically, so it’s important to recognize that OSHA penalties for a “Serious” violation of a safety standard can reach $16,131 as of 2024. And a “Willful” violation can carry fines 10x that amount, per violation. While MSHA’s penalties can range from a couple hundred dollar, on up to $323k for each violation, the Office of Assessments calculates penalties according to a formula that considers 5 factors:
1. history of previous violations
2. size of the business
3. any negligence by the operator
4. gravity of the violation
5. the operator’s good faith in trying to correct the violation promptly
In cases involving extreme danger or willful violations, the Office of Assessments may also determine that a higher Special Assessment is appropriate.
Lost Time and Productivity
When a workplace accident happens, operations come to a standstill. Before work can resume, injured workers must be cared for, an initial investigation must be performed, and machinery and equipment must be inspected for proper functionality. Sometimes, the involved areas or machines must be cordoned off or taken out of service until a detailed investigation can be performed. And in some instances, such as a serious injury or fatality, the entire operation may cease for a period of time.
When your employees sustain injuries, there's a likelihood that their ability to work will be compromised. They may be out of work altogether for a time, meaning you’ll have to recruit and train temporary staff, offer overtime to other employees, or accept reduced production. However, an inexperienced worker will likely not match the productivity of the injured employee.
Time lost here is not just for those injured, but also many others that play a part in the reactive duties and measures associated with the event. HR, Safety, and/or Management personnel will spend time working through the claim with the insurance company, creating new schedules to accommodate missing employees, investigating the incident causes, filling out paperwork and drafting reports, cooperating with regulators, and implementing preventative measures. All these tasks consume hours and retract from the time these professionals could be spending on efforts in the field.
Indemnity Costs
Should investigations reveal that a company’s failure to comply with safety regulations resulted in the injury or fatality, the company may incur costs for:
· Third-party Investigation
· Legal Services
· Court Fees
· Death or Disability Compensation
· Dependent Benefits
· Settlements
Morale and the Emotional Toll
The trauma of a serious accident can be difficult for all employees. The emotional toll of an injured or deceased coworker can psychologically impose a lack of motivation and worse, a loss of focus, which can increase the likelihood of subsequent injuries. When employees do not feel that leadership is capable or willing to make the workplace safe, morale declines significantly. In environments where morale has degraded, employees are far more likely to demonstrate higher risk tolerances, reduced productivity, and report safety violations to regulators without giving the company an opportunity to correct it.
Reputation
Both MSHA and OSHA provide a publicly accessible database, where anyone can view citations, injury rates, and fatality records of any company. Which can cause unquantifiable harm to a company’s reputation.
Poor morale, if left uncorrected, causes employees to seek employment elsewhere, and warn other potential candidates not to consider employment with the company, by word-of-mouth. Many industry and trade forums online nowadays demonstrate exactly this, as the (often negative) opinions of current and previous employees are shared. And the picture that is painted by employees when regulators talk with them about their employer is not a positive one. This commonly results in higher penalties as employees volunteer harmful and sometimes inaccurate information to regulators as they vent emotionally.
These components can repel clients, investors, and job candidates. Quality safety professionals and other experienced leaders who can positively impact the business, choose not to apply, or ultimately decline the positions, necessitating the need to hire or promote inexperienced candidates. A poor safety reputation can also negatively impact state and federal agency decision makers, when approving permits, licenses, and other authorizations that are crucial to a company’s growth or continued operation.
So, what is the cost?
The cost of accidents themselves, as you can see, is a very difficult thing to quantify, and is going to vary greatly from business to business and accident to accident. But we can get a bit of a peek by taking some of the data we know. We know the average expense for workers' compensation claims is projected at $41,353. A study conducted by Harvard University, Liberty Mutual Research Institute of Safety, and the University of Wisconsin Oshkosh, there is approximately $2.12 in indirect costs for every $1 of direct cost, on average for a workplace accident.
Direct Costs = $41,353
Indirect Costs = (41,353 x 2) = $87,668
Total = $41,353 + $87,668 = $129,021
A total cost of $129,021/accident and we aren’t even considering the harm to, or consequences of, the effects on workforce morale, emotional health, or company reputation.
Business Owners and Managers, I challenge you to take this number and multiply it by the number of accidents you had last year. Is the sticker shock of that new proposed safety program starting to wear off?
Safety Professionals and Trainers, multiply this by the number of incidents that had the potential to be more serious. Then multiply it by the number of near-misses and share that information with leadership teams.
Solution
We all recognize that we are moving into a time where the experience of one generation is leaving the workforce, and a knowledge gap is being left. Employee education, supportive mentorship, and employee involvement are some of the best approaches to filling this gap in a positive and productive way. Employers who invest in their employees’ knowledge, and support their insight and innovation are regarded by employees as a company that cares. They feel like they are part of the company, instead of just there for the company’s use. More importantly, they believe in a future, not only with the company, but also a future FOR the company, and that’s where visions converge to become the driver of success.
info@relsafety.com
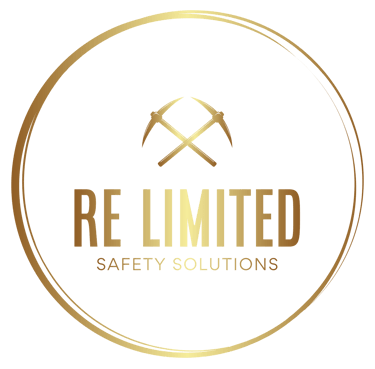
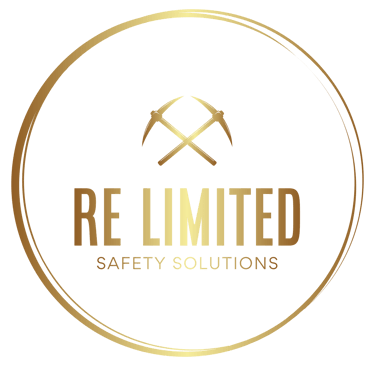